Part # 17-758? I ordered a few of those today, I did not realize I labeled them wrong. I don't think that I broke it, I didn't drop / force anything. When it came out it was shorter than the rest. I'm not sure.The "guide pins" as you call them are the plastic 1/4'Diameter that fit into the outer bearing retaining ring
and stop the rod end bearings clattering onto the swash plate housing six (6) in total 2 per rod end bearing. This is not the part your want stop calling it a guide pin you will confuse the natives.
The "tiny" stainless pins your describing are part number 17-757 Pin, Valve
Granted its known to the rest of the world and most engineers as a dowel pin
but Pin, Valve describes the application better as far as the product is concerned.
Dowel Pin. Heat treated stainless steel hardened 1/32" diameter x 1/4" long
per ANSI ASME B18.82 standard series base diameter if you want the full description.
Granted they are small I wouldn't say tiny its not a watch part just don't drop them on a rolling deck in the dark I guess LOLIain
There was a guy that posted a while back that he would make some videos about the heads... not sure whatever happened there but I bet if he did that I wouldn't have gotten so much wrong!

I did use a razor blade for the last little bit, but mostly I used a hard plastic scraper.Heck? That what a steel razor blade or Stanley knife blade is for. If the gasket is suck on the stainless valve plate scrap the old gasket off with the razor blade getting it under the hardened gasket and only if required lap the valve plate with a fine 600 -1200 grit wet and dry or if in doubt use Brasso a brass polish on a flat glass plate (just clean the paste off well after) Don't scratch the valve plate or dig chunks out of it.
I use an old Buck rosewood handled knife for the purpose but that's classed as a luxury tool now a days
If the gasket is stuck inside the aluminium head again I use an old Parker brass flat blade end of a O Ring pick tool (sharpened) Its also used for lifting rings and removing piston o rings
I have those and could have used them but it seemed just as easy to line the holes up.To line up the valve onto the dowel pin discharge side I use a pair of Waldes Truarc straight circlip pliers (old school) if I was buying new today I would use a pair of Knipex Straight circlip pliers 3-10mm
The essential part you need to be aware is only poke them into the holes that are on the recessed half of the valve that way you don't "form" the holes on the ground flat side half and cause the reed valve to leak over your created raised edge.
This also ensures you don't fit the valve upside down or you will blow yourself up.
Use this principle for both the 3rd and 2nd stage you should also note that the hole you're grouping for is in line with the valve head body mounting holes.
Snapping the dowel pin by janking the valve around "looking" for the hole to fit the valve body into the dowel pin will make it shorter yes just try not doing that in future.Iain
How imperative is it to have lube on the o ring? Mine came with none. Maybe just a little to make things slide together easier?
Well.. I did post a list of parts in this thread that I thought I needed for the rebuild. I went off of the manual and I even called Rix to see if they thought I needed anything else.The pressure breaker rings are a matching pair and should be in a small plastic bag. Don't swap the halves over with another matched pair or you end up with two mis matched pairs.
You also should have asked this question before ordering these rings, We stopped using them some time back at the Skunk works and use for our current builds just two additional pairs of compression rings instead.
Talk about the right hand nor knowing what the left is doing.
All you need to remember is Rule 1. Engineers rule.
On the bright side after your 3 month wait you saved yourself $2 I guess.Iain
I would have preferred to do it right and not have to have waited the 3 months.
If the "new" way is to just add another 2 compression rings then why are we all still passing around an outdated manual? Heck, that's even the same manual that Rix sent me in ~ Oct. when I placed the order?
You can see in this pic that there's no way I can fit that in there. Rix told me tolerances for that part are .070-.073. The slots on my piston measure .072 and .069 wide. How come they're out of spec (or maybe they're not and things have changed?)? And to top it off, one of the halves measures .075, so it's out of spec.
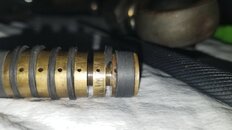
I'll echo @-JD- , do they get o rings underneath if using regular compression rings?
So no o ring, but used to be one, but shouldn't get one because it will throw the weight off.. got it... clear as mudIt did have an o-ring but years ago I will pull up the part number for the old rider ring 0-ring when back at the works It was a carry over from the SA-6A
The reason the groove is still machined is because changing the cad drawing and dfx file for the CNC is much too complicated for highly paid engineers.................Nah just kidding
The other reason is keeping the piston groove is consideration to the "weights" in balance on the swash plate running at 1500 RPM on a 32mm stroke. Consideration to the mass weight acceleration and deceleration at TDC and the need to match the weight transfer over the other two pistons over the piston stroke over the travel length.
If by way of example you were to change the gas molecular weight or say you want to change to nitrox
engineering considerations would require changing from a fully aluminium piston to say a bronze lip design and that additional weight flying about would have effect. Now for ease you could consider say more grooves or deeper grooves in the piston or a scooped out back to lighten the weight to match the original weight etc etc hence why if you have no change in gas or pressure or rod loading and no real need for the o-ring itself it was removed but the groove remained for the purpose of weight reduction.
Clear as mud I know but one day I may learn to give better explanations.Iain

I do appreciate your posts!