Here is the aftermarket secondary filter and fill whip I attach to the 130R1500 during use (Note that I keep the inlet hose plugged to prevent unnecessary atmospheric moisture from entering the system when off season or not in use). I remember seeing that your setup came with a secondary filter and fill whip, which, along with the 130R1500 itself, were attached to a secondary base, if I remember correctly.
The filter housing itself has a condensation drain at its bottom, but the separator on the 130R1500 is so efficient (when a proper back pressure valve is used) that the most I ever get from the secondary filter when opening the drain valve is maybe a one second burst of light mist, even when the filter housing was sitting in cold water while operating.
Inside the filter housing is an old Bauer filter cartridge which is refillable. This cartridge holds about 1/2 shot of activated carbon (activated charcoal) and one shot of Lawrence Factor Vaporshell 13X molecular sieve, these media being separted by and sandwiched between discs made of polyester filter sheet.
The media change frequency for the size of my setup was recommended to be every 1600-2000 cubic feet of air flow. I have never reached that amount in a year, so I change it annually just to be safe.
Filter housing disassembled, showing refillable filter cartridge:
Open end of refillable cartridge:
Last, but CERTAINLY NOT LEAST (It is one of the most important features necessary for efficient filtering) is a BACK PRESSURE VALVE. The separator and dessicant work most efficiently when under pressure. So, if no back pressure valve is in the system behind the filtration, the first half or so of your fill of an empty tank will be inefficiently filtered. The 130R1500 itself has no back pressure valve, and even if it did it would not help the efficiency of the secondary filtration.
My secondary filter has a built-in pack pressure valve. It is adjustable via a screw on the top of the housing:
I have mine set to 1500 psi, but was told by a man at Lawrence Factor that it would be better to set at 1700-2000 psi. The idea is that the higher, the better, but you don't really want your compressor working against 3000 psi all of the time. So, the lowest setting necessary for acceptable efficiency will help save your compressor from unnecessary wear while giving good, dry fills.
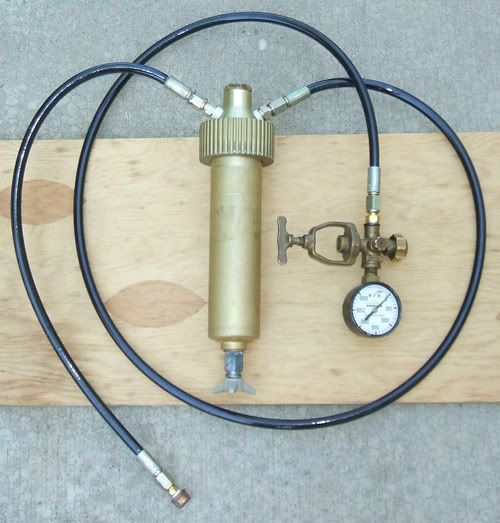
The filter housing itself has a condensation drain at its bottom, but the separator on the 130R1500 is so efficient (when a proper back pressure valve is used) that the most I ever get from the secondary filter when opening the drain valve is maybe a one second burst of light mist, even when the filter housing was sitting in cold water while operating.
Inside the filter housing is an old Bauer filter cartridge which is refillable. This cartridge holds about 1/2 shot of activated carbon (activated charcoal) and one shot of Lawrence Factor Vaporshell 13X molecular sieve, these media being separted by and sandwiched between discs made of polyester filter sheet.
The media change frequency for the size of my setup was recommended to be every 1600-2000 cubic feet of air flow. I have never reached that amount in a year, so I change it annually just to be safe.
Filter housing disassembled, showing refillable filter cartridge:
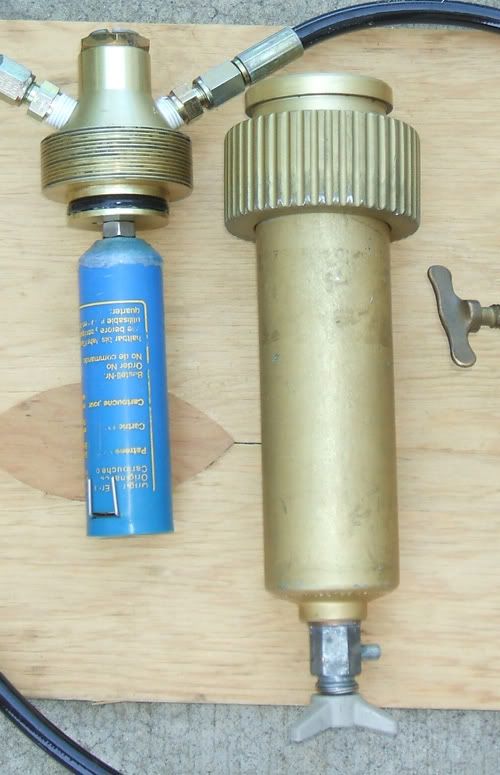
Open end of refillable cartridge:
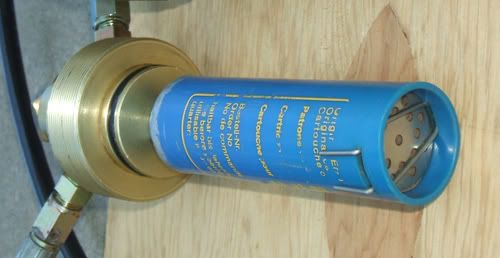
Last, but CERTAINLY NOT LEAST (It is one of the most important features necessary for efficient filtering) is a BACK PRESSURE VALVE. The separator and dessicant work most efficiently when under pressure. So, if no back pressure valve is in the system behind the filtration, the first half or so of your fill of an empty tank will be inefficiently filtered. The 130R1500 itself has no back pressure valve, and even if it did it would not help the efficiency of the secondary filtration.
My secondary filter has a built-in pack pressure valve. It is adjustable via a screw on the top of the housing:
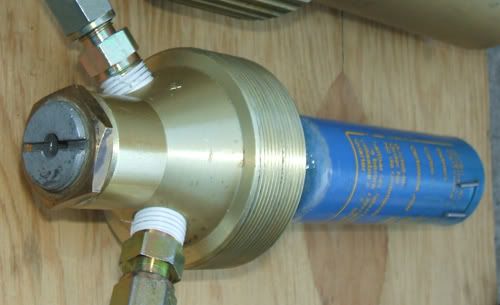
I have mine set to 1500 psi, but was told by a man at Lawrence Factor that it would be better to set at 1700-2000 psi. The idea is that the higher, the better, but you don't really want your compressor working against 3000 psi all of the time. So, the lowest setting necessary for acceptable efficiency will help save your compressor from unnecessary wear while giving good, dry fills.
Last edited: