Hi, everybody
I come here with a recent problem I had with a tank, brand BTS (also known as EUROCYLINDERS), that I bought in a Dive Shop in Tenerife (Spain) in January 2011.
It´s a 12 litres steel tank, with double valve, with manufacture date AUGUST 2010.
On first days of January 2012 I sent it to the authorized place for the mandatory annual Visual Inspection.
The out side of the tank is this:

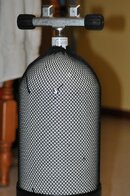
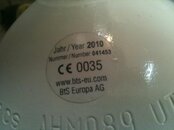
And this is what the techniccian found when he opened it. He inmediately called to go and check it, telling me he had never seen a tank in these conditions with that manufacturing date and that the cylinder has a manufacture fail.
These are the pics:
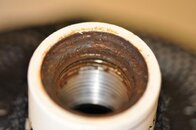
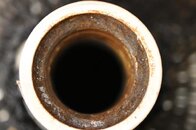
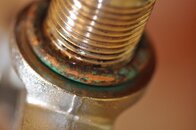
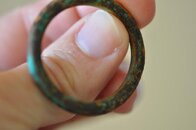
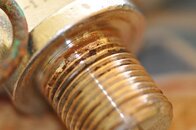
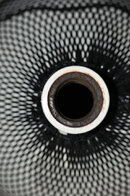
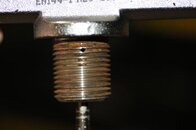
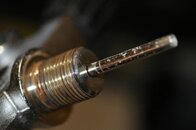
The tanks has around 40 dives, has been always charged in 2 authorized charging stations, where I go with my other tank - different brand- that was perfect in the same Visual Inspection.
Never has been empty and I washed it often in unsalted water.
I can´t show pics from the inside of the cylinder, but it was completely oxidated, from the top to the bottom.
When we put it down, this is what came out from inside:
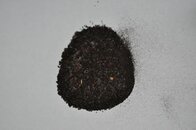
And these are some of the oxide marks outside the tank. As you can see in the pics they are not due to scratches:
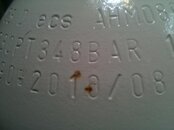
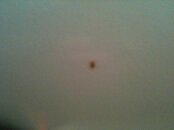
The dive shop where I bought it denies any responsability (in fact they didn´t even take note of the serial number of took any pictures when I was there with it during more than half an hour), even the tansk is IN GUARANTEE, arguing that
all is my fault beause of wrong done tank charges. Next day I send them a photo with the serial nº ... that was around twenty day ago.
I wrote to BTS Europa using the ¨contact¨ menu of their web page on Saturday, 28 January... NO ANSWER
I need some help from the forum... What should I do now??????????
thanks
I come here with a recent problem I had with a tank, brand BTS (also known as EUROCYLINDERS), that I bought in a Dive Shop in Tenerife (Spain) in January 2011.
It´s a 12 litres steel tank, with double valve, with manufacture date AUGUST 2010.
On first days of January 2012 I sent it to the authorized place for the mandatory annual Visual Inspection.
The out side of the tank is this:

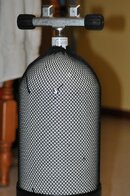
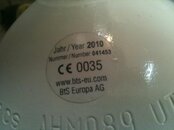
And this is what the techniccian found when he opened it. He inmediately called to go and check it, telling me he had never seen a tank in these conditions with that manufacturing date and that the cylinder has a manufacture fail.
These are the pics:
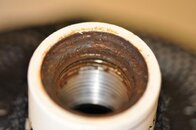
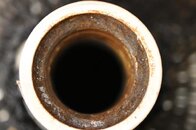
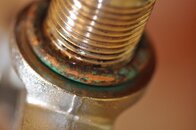
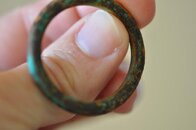
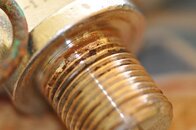
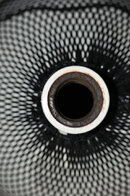
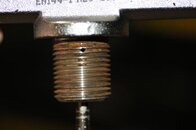
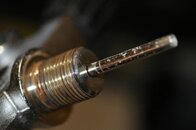
The tanks has around 40 dives, has been always charged in 2 authorized charging stations, where I go with my other tank - different brand- that was perfect in the same Visual Inspection.
Never has been empty and I washed it often in unsalted water.
I can´t show pics from the inside of the cylinder, but it was completely oxidated, from the top to the bottom.
When we put it down, this is what came out from inside:
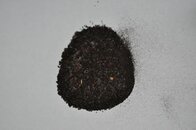
And these are some of the oxide marks outside the tank. As you can see in the pics they are not due to scratches:
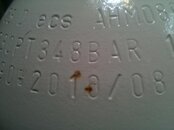
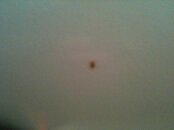
The dive shop where I bought it denies any responsability (in fact they didn´t even take note of the serial number of took any pictures when I was there with it during more than half an hour), even the tansk is IN GUARANTEE, arguing that
all is my fault beause of wrong done tank charges. Next day I send them a photo with the serial nº ... that was around twenty day ago.
I wrote to BTS Europa using the ¨contact¨ menu of their web page on Saturday, 28 January... NO ANSWER
I need some help from the forum... What should I do now??????????
thanks