the_dragon_no1
Contributor
Hello everyone !
I have started makeing a housing for my cam. take a look at the pic's and feel free to post ideas, or questions :cool2:
will try to use flat rubber gasket between the lins part and the house itself.. might have to go for a O-ring :?
-glue i have used is 2k epoxy, and on small parts inside, i have used regular superglue.
-main plexi is 11mm thick.
-will be useing stainless steel latches. (ordered)
-will be useing "Ikelite" control glands (ordered)
-the two handles, is from angle grinders
-i will also order a wireless flash soon, and build a flex arm, and housing for it aswell
-"wing" plate under is from real carbonfiber.:cool2:
Got one problem so far.... mounting the plexi in front of the lens, to the pipe, without gluing it ( if i realy dont have to) any good ideas please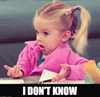
the "support" pipe inside the black lens pipe WILL be glued with pvc glue. as now, glass and "support" pipe is moveble inn/out.
i was gonna use a pvc end cap(cut out center), with latches on, BUT, they dont make the size i need i think
aprox 82mm inside, btw.
(pictures is not in order)
I have started makeing a housing for my cam. take a look at the pic's and feel free to post ideas, or questions :cool2:
will try to use flat rubber gasket between the lins part and the house itself.. might have to go for a O-ring :?
-glue i have used is 2k epoxy, and on small parts inside, i have used regular superglue.
-main plexi is 11mm thick.
-will be useing stainless steel latches. (ordered)
-will be useing "Ikelite" control glands (ordered)
-the two handles, is from angle grinders

-i will also order a wireless flash soon, and build a flex arm, and housing for it aswell

-"wing" plate under is from real carbonfiber.:cool2:
Got one problem so far.... mounting the plexi in front of the lens, to the pipe, without gluing it ( if i realy dont have to) any good ideas please
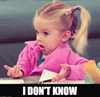
the "support" pipe inside the black lens pipe WILL be glued with pvc glue. as now, glass and "support" pipe is moveble inn/out.
i was gonna use a pvc end cap(cut out center), with latches on, BUT, they dont make the size i need i think

(pictures is not in order)
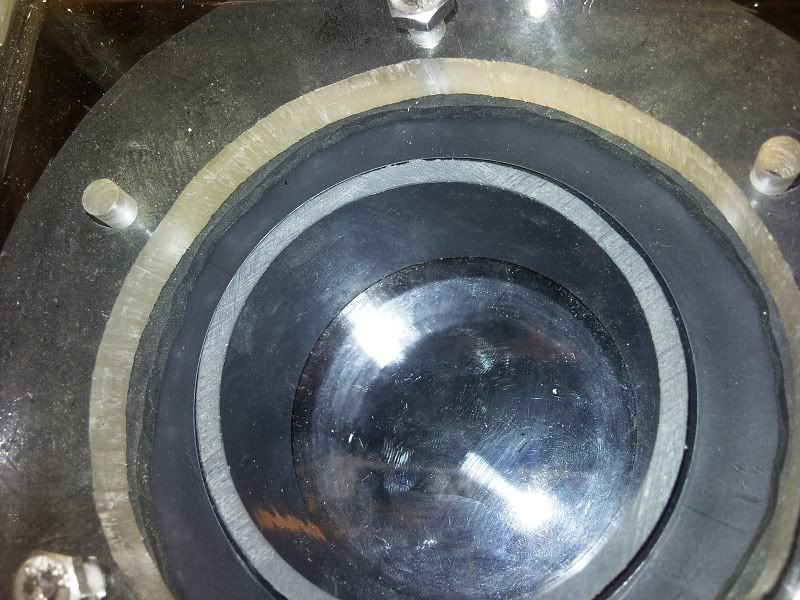
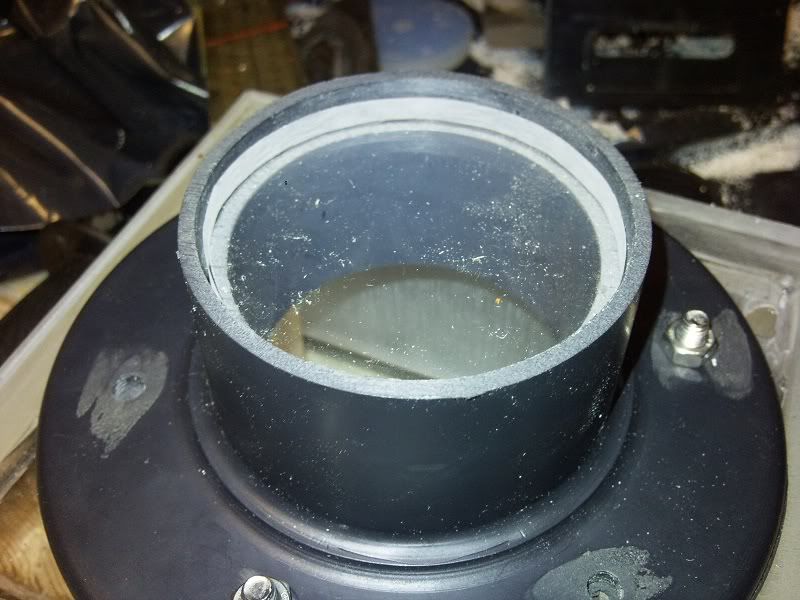
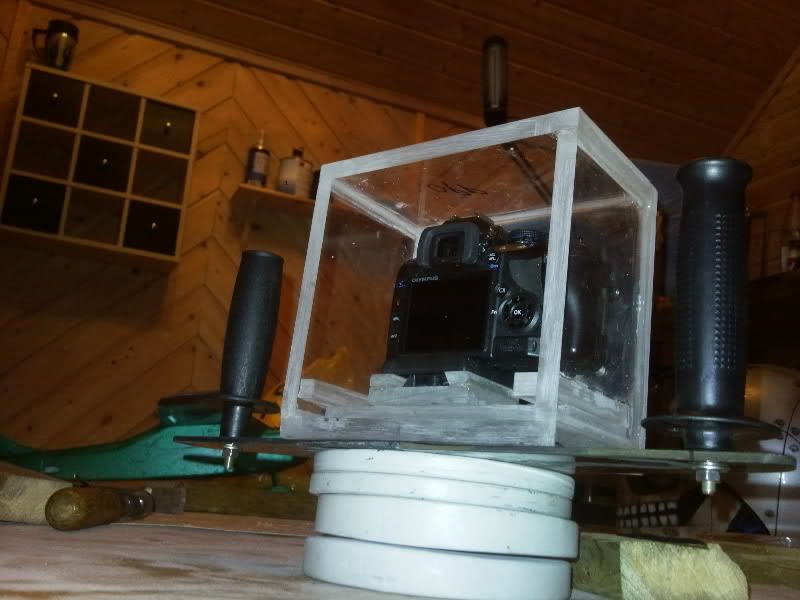
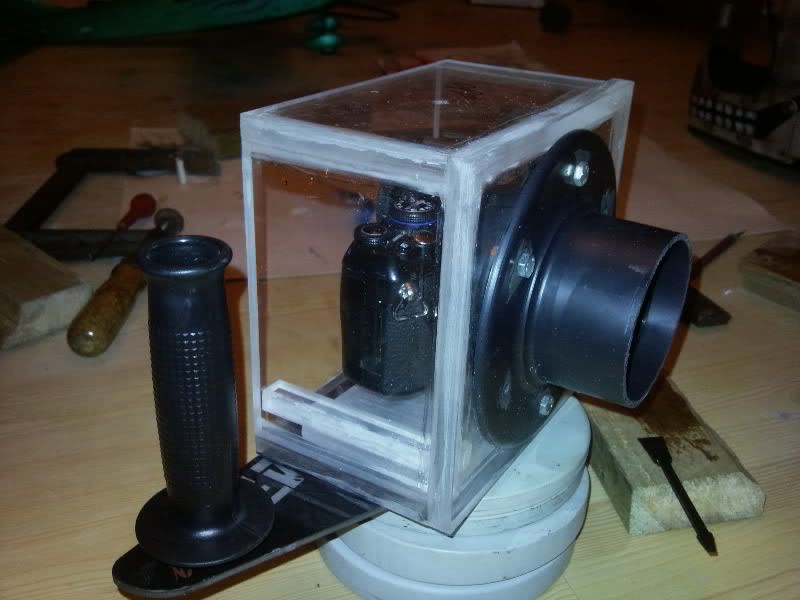
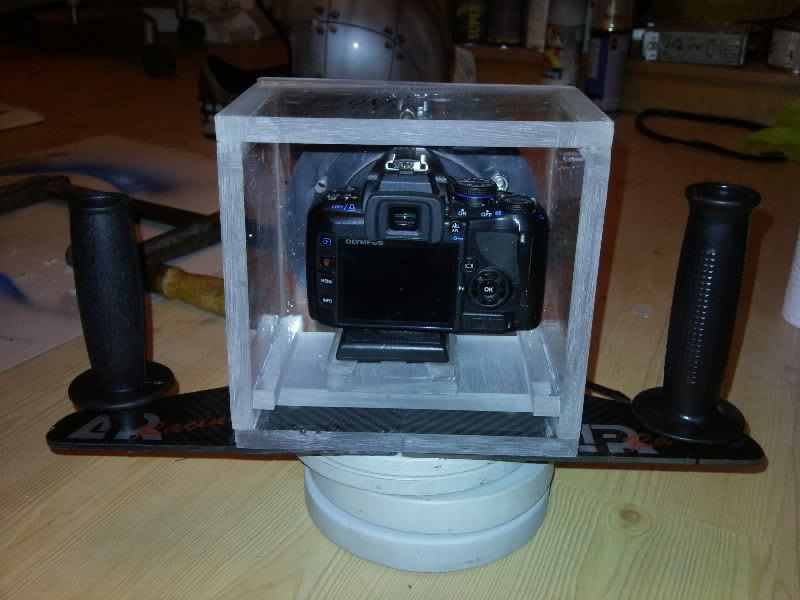
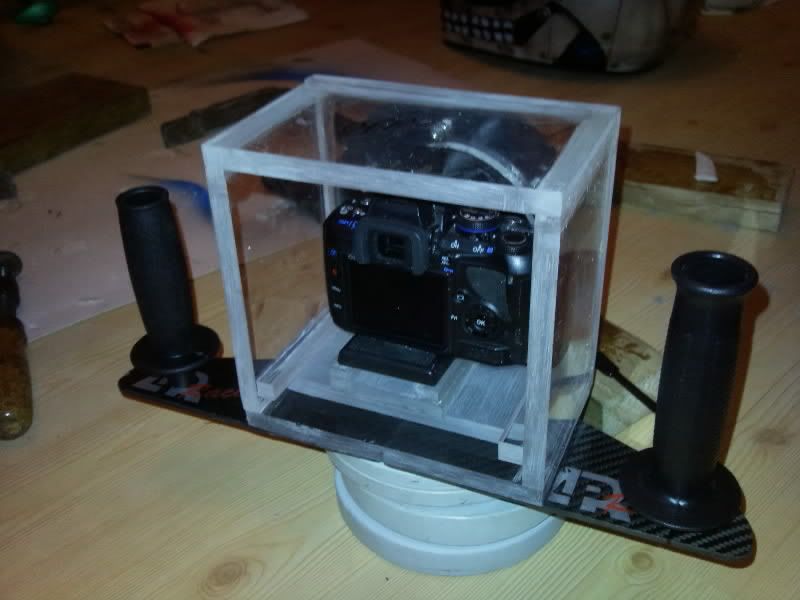
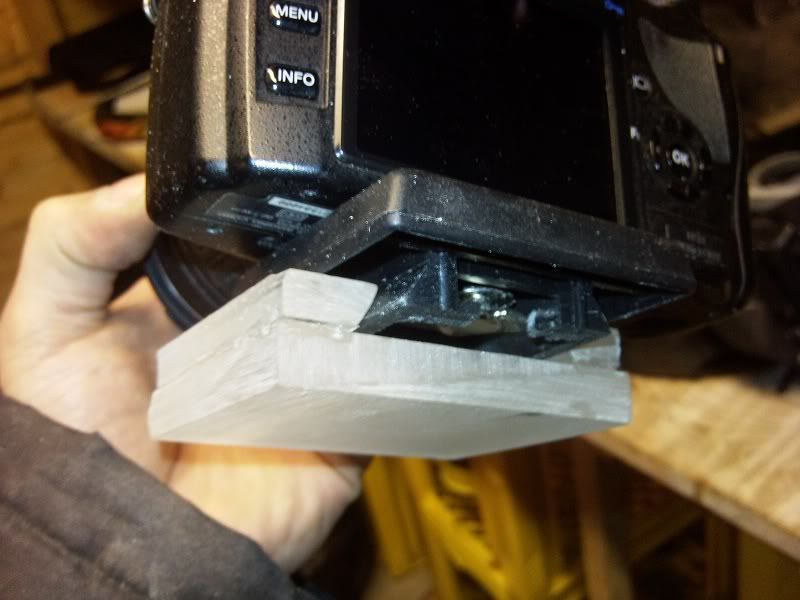
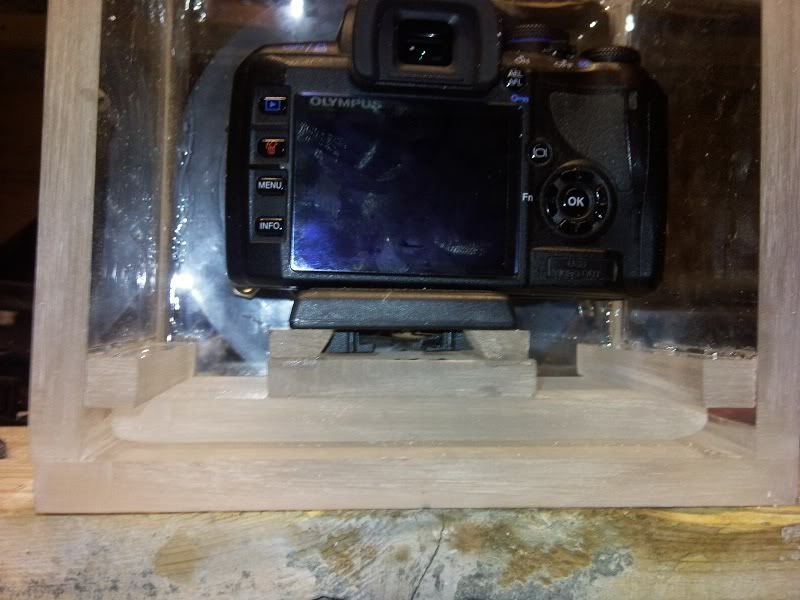
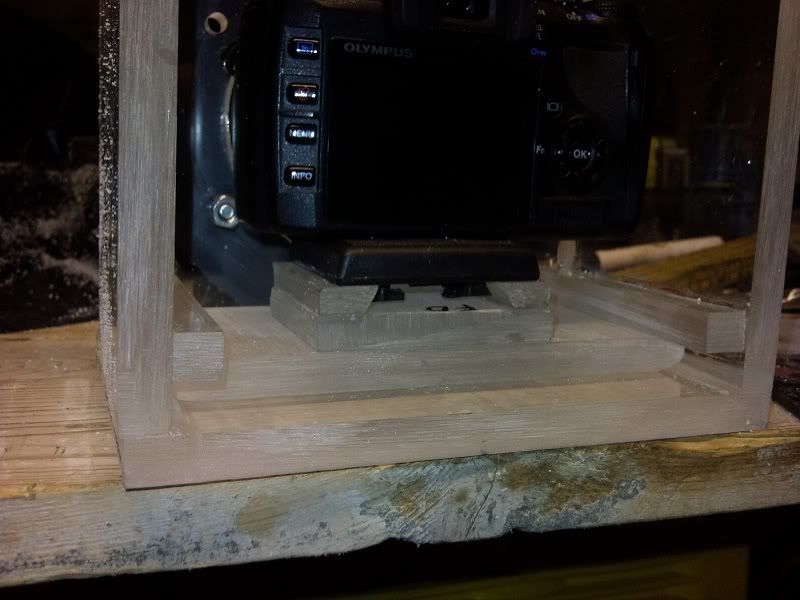
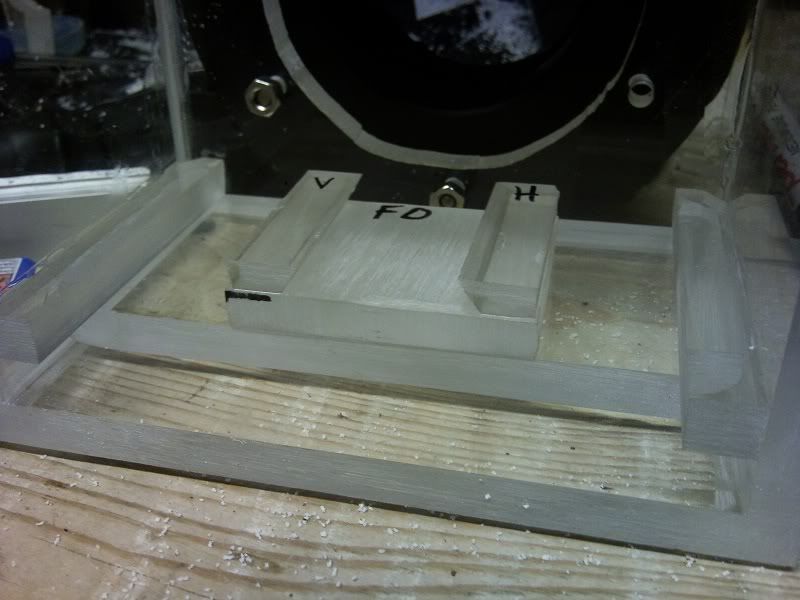
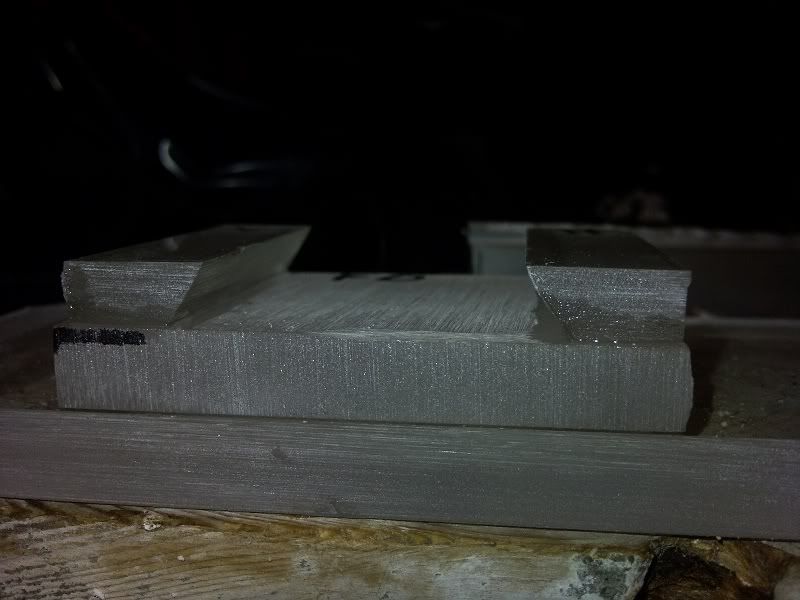

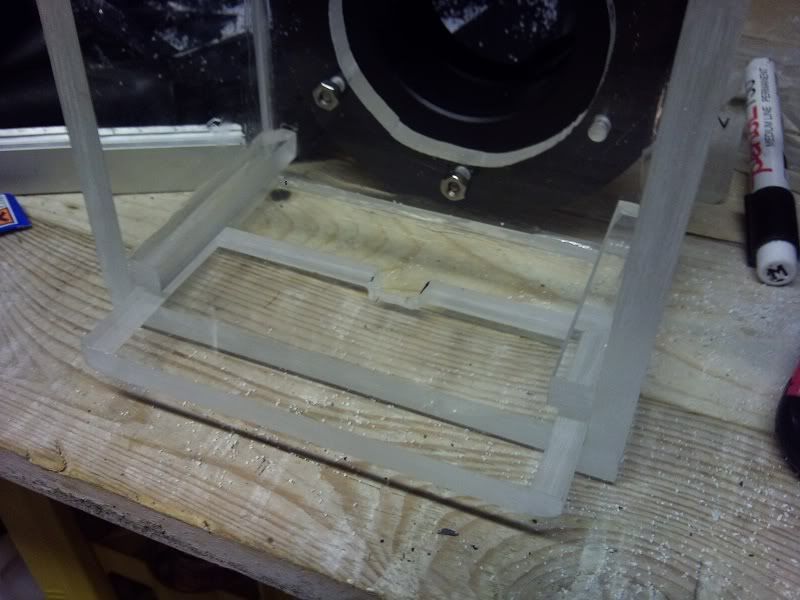
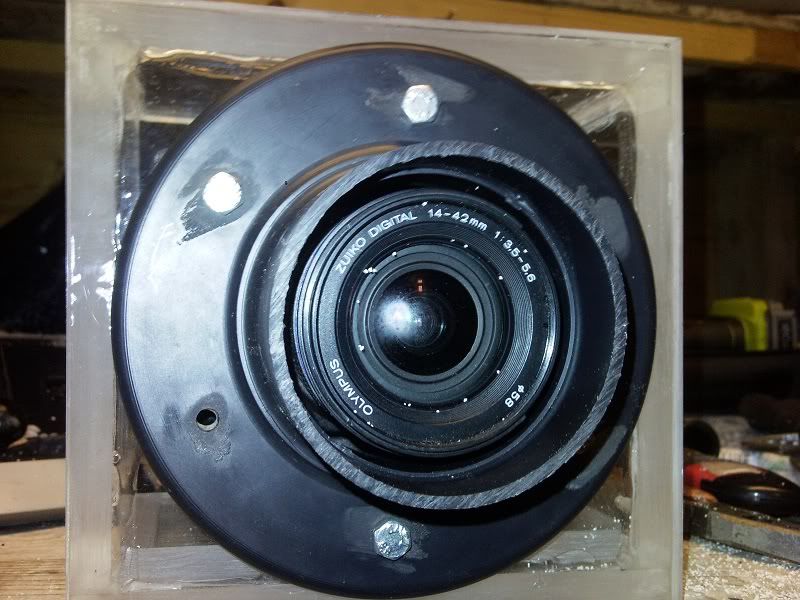
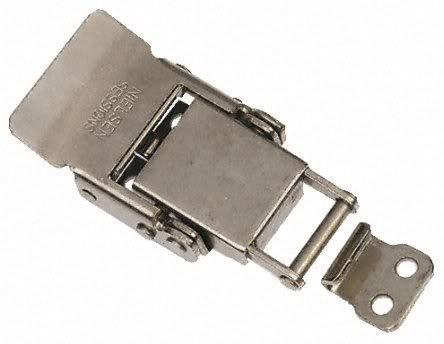
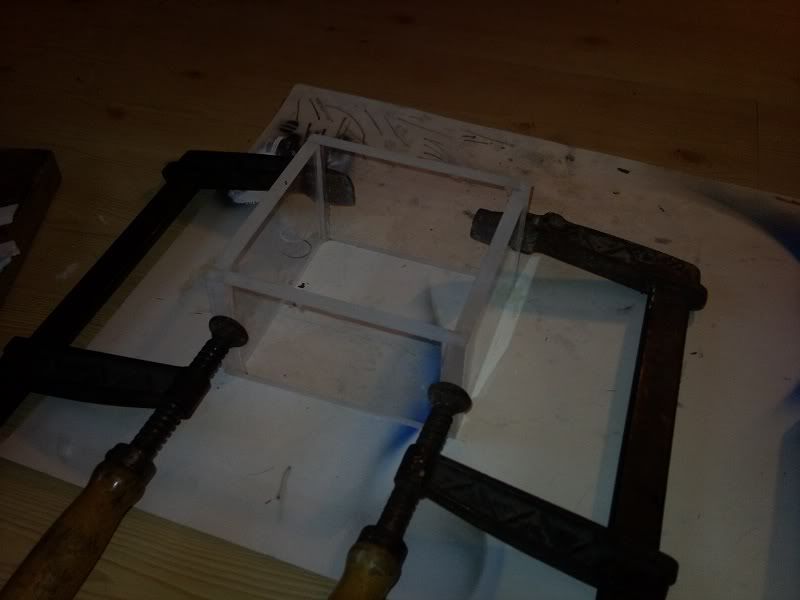
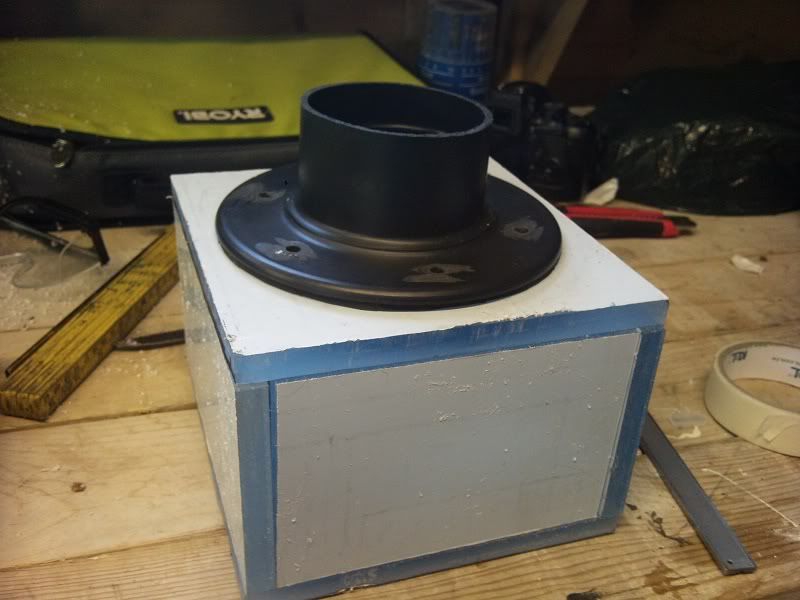
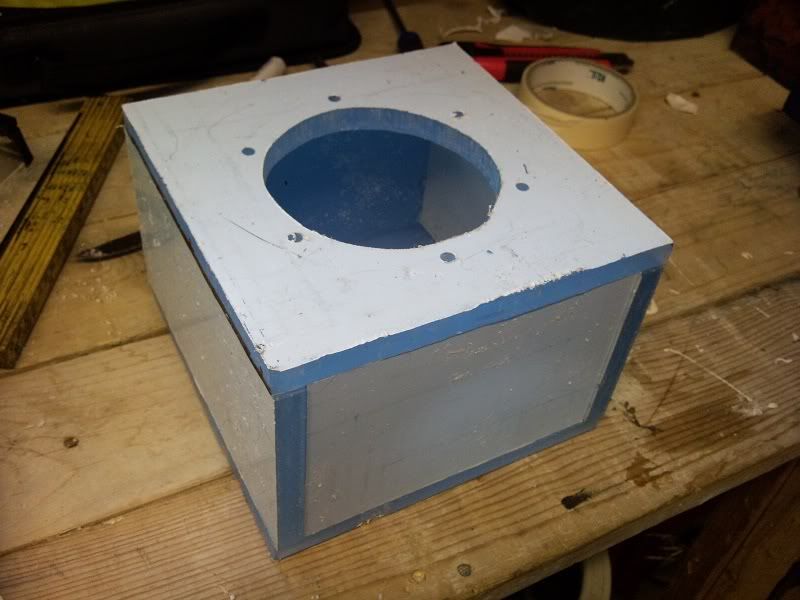
