tmassey
Contributor
Say hello to the newest member of my family!
What do you mean I have an ugly baby?
It's a well-used Haskel AGD-7 that I just received from eBay. Supposedly it was "tested and working". I guess we'll see. And yes, it's pretty ugly.
I've got zero experience with boosters. I've seen one in operation exactly twice. So, before I do something stupid and break it (or me!), I'm here for advice. I own a SCUBA compressor and have some small experience with high-pressure gas so I don't overly need the most basic generic safety information, though I'm happy to be reminded, too. Anything Haskel/booster specific, though, and you should assume I know nothing.
Let's start operationally: what do I need to check out before I hook up gas to this thing? Any tests I should perform? Any suggestions to do -- or not do -- to start this guy operating? How can I verify that it's working like I could or should expect it to?
One specific question: the drive gas outlet has the elbow, but seems to be missing whatever device goes on the end of the elbow. What is that, and do I need it? I'm hoping it's something like, say, a muffler that I might want to have but I'll be OK today without it. But please let me know!
Then, let's talk cleaning. This will only pump inert gas, so I'm not worried about O2 clean. What I *am* worried about is breathing-gas clean. What can be done to make sure what it pumps won't kill me? I don't mean air-quality testing: I know about that. I mean is there something I can do to visually/otherwise check on this thing, or is there a way to proactively clean it?
While we're talking clean: the outside is pretty sad-looking. Any suggestions about how to safely and effectively spruce this thing up? (I'm hoping the inside isn't quite as sad-looking...)
I know it's a baby booster, better for rebreather tanks than OC doubles. The 2500 PSI maximum and 7:1 boost ratios are both tricky. But doing the math, it seems it will just barely meet my worst-case, which is pushing 1200 PSI of helium on top of 1200 PSI of 18/45 to let me make 3600 PSI of 18/45, from an equalized supply pressure of 1600 PSI. I realize it will do so slowly and using a fair amount of drive gas: from the chart at Haskel model AGD-7 Double-Acting, Single-Stage Gas Booster it seems that drive gas will be roughly 120% of boosted gas volume, so something like 100 CF.
I can live with that. I doubt I'll be doing that worst-case more than two or three times a year *tops*. The nice thing is that I use a set of SCUBA doubles as my helium storage bottles, so I don't need to worry about supply pressures lower than 1200 PSI. When the source gets to that point, I add EAN32 on top and go dive them!
Here are some thoughts on how I plan on setting this up. Initially, I plan on using a 444 ft3 bank bottle filled with air (from my SCUBA compressor), connecting a SCUBA first stage and using a a LP port to connect to the booster. Initially, I plan on putting a needle valve in there for initial testing and operation. Once I have a better idea of how this works, the intention would be to investigate a shop air compressor instead of using my poor SCUBA compressor to supply glorified shop air. But as I don't own a shop air compressor at this time, I'll start with what I've got. Given the frequency that this thing will be used at this time (not much), I'm not in a rush right now.
The source/destination ports would be plumbed with via Parker ST quick connects (like the rest of my compressor configuration uses). Both the source and the destination would then terminate in hoses and DIN filler adapters: one connected to the doubles that contain pure helium, and the other to the set of doubles I'm blending trimix into. (Same type of setup I use with my O2 (Argox) concentrator/compressor, nitrox stick, deco bottles, etc. Works really pretty well.)
Honestly, my idea with this was largely to get started with Haskel ownership and experience. I made a fairly low-ball offer and was surprised when it was accepted. But I certainly don't want to have to sink a bunch of money into it, which is why I'm looking for advice. I've got 30 days to determine if it's what I was told it was -- a "tested and working" booster. If it is, I'm OK with the limitations. If I need more down the road I can always re-sell it and upgrade to something bigger then.
Thank you for any help you might be able to provide! I really appreciate it.
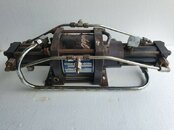
What do you mean I have an ugly baby?

It's a well-used Haskel AGD-7 that I just received from eBay. Supposedly it was "tested and working". I guess we'll see. And yes, it's pretty ugly.
I've got zero experience with boosters. I've seen one in operation exactly twice. So, before I do something stupid and break it (or me!), I'm here for advice. I own a SCUBA compressor and have some small experience with high-pressure gas so I don't overly need the most basic generic safety information, though I'm happy to be reminded, too. Anything Haskel/booster specific, though, and you should assume I know nothing.
Let's start operationally: what do I need to check out before I hook up gas to this thing? Any tests I should perform? Any suggestions to do -- or not do -- to start this guy operating? How can I verify that it's working like I could or should expect it to?
One specific question: the drive gas outlet has the elbow, but seems to be missing whatever device goes on the end of the elbow. What is that, and do I need it? I'm hoping it's something like, say, a muffler that I might want to have but I'll be OK today without it. But please let me know!
Then, let's talk cleaning. This will only pump inert gas, so I'm not worried about O2 clean. What I *am* worried about is breathing-gas clean. What can be done to make sure what it pumps won't kill me? I don't mean air-quality testing: I know about that. I mean is there something I can do to visually/otherwise check on this thing, or is there a way to proactively clean it?
While we're talking clean: the outside is pretty sad-looking. Any suggestions about how to safely and effectively spruce this thing up? (I'm hoping the inside isn't quite as sad-looking...)
I know it's a baby booster, better for rebreather tanks than OC doubles. The 2500 PSI maximum and 7:1 boost ratios are both tricky. But doing the math, it seems it will just barely meet my worst-case, which is pushing 1200 PSI of helium on top of 1200 PSI of 18/45 to let me make 3600 PSI of 18/45, from an equalized supply pressure of 1600 PSI. I realize it will do so slowly and using a fair amount of drive gas: from the chart at Haskel model AGD-7 Double-Acting, Single-Stage Gas Booster it seems that drive gas will be roughly 120% of boosted gas volume, so something like 100 CF.
I can live with that. I doubt I'll be doing that worst-case more than two or three times a year *tops*. The nice thing is that I use a set of SCUBA doubles as my helium storage bottles, so I don't need to worry about supply pressures lower than 1200 PSI. When the source gets to that point, I add EAN32 on top and go dive them!

Here are some thoughts on how I plan on setting this up. Initially, I plan on using a 444 ft3 bank bottle filled with air (from my SCUBA compressor), connecting a SCUBA first stage and using a a LP port to connect to the booster. Initially, I plan on putting a needle valve in there for initial testing and operation. Once I have a better idea of how this works, the intention would be to investigate a shop air compressor instead of using my poor SCUBA compressor to supply glorified shop air. But as I don't own a shop air compressor at this time, I'll start with what I've got. Given the frequency that this thing will be used at this time (not much), I'm not in a rush right now.
The source/destination ports would be plumbed with via Parker ST quick connects (like the rest of my compressor configuration uses). Both the source and the destination would then terminate in hoses and DIN filler adapters: one connected to the doubles that contain pure helium, and the other to the set of doubles I'm blending trimix into. (Same type of setup I use with my O2 (Argox) concentrator/compressor, nitrox stick, deco bottles, etc. Works really pretty well.)
Honestly, my idea with this was largely to get started with Haskel ownership and experience. I made a fairly low-ball offer and was surprised when it was accepted. But I certainly don't want to have to sink a bunch of money into it, which is why I'm looking for advice. I've got 30 days to determine if it's what I was told it was -- a "tested and working" booster. If it is, I'm OK with the limitations. If I need more down the road I can always re-sell it and upgrade to something bigger then.
Thank you for any help you might be able to provide! I really appreciate it.