OkByMe
Contributor
- Messages
- 599
- Reaction score
- 202
- # of dives
- 500 - 999
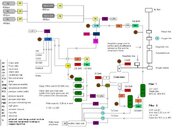
ALKIN W31 - 2006
Weight 125lbs. with all accessories.
240 volt 4 wire 1 phase power.
1200 R.P.M.
4500PSi service pressure with 3 stage filtration.
Adjustable pressure switch for compressor shut down at selected pressure, in this case, 4500psi.
Auto-dump 3 stage condensate drains with accumulator tank and sound muffler.
Dump between 1st. and 2nd. stage
dump at 1st filter
dump at 2nd. filter
High and low pressure manifolds.
Intake designed for NITOX and TRI-MIX with turbulator.
Differential Magnahelic guage in intake to monitor pressure/vacuum. (+/- 3psi)
Oxygen shut off relay to stop oxygen flow when compressor stops.
Oxygen sensor mounted after turbulator unit.
Flexible cascade connect (6,000psi) hose with quick dis-connect from high pressure manifold with control valve.
Check valve mounted between 1st. filter and compressor 3rd. stage output line to isolate 1st. filter at compressor shutdown.
Priority valve mounted after 1st. filter output to 2nd. filter. (1800psi. set)
check valve mounted after 1st. filter priority valve before 2nd. filter.
Priority valve mounted after 2nd. filter to high pressure manifold. (1800psi. set)
Check valve installed in the compressor feed line after 2nd. filter priority valve to the high pressure manifold preventing cascade from pressurizing compressor and/or filters - stop reverse flow.
Carbon Monoxide and moisture sensor on 2nd. filter output to high pressure manifold.
Flow control valve from high pressure manifold to pressure regulator for low pressure manifold.
3 way valve on low pressure manifold to isolate 3rd. filter bank (when not using breathing air fill) with Pressure relief valve to 3500psi just in case 3 way valve selects filter and regulator is set above MOP for stack.
Check valve on 3rd. filter bank output to low pressure manifold to prevent reverse flow through filter when charging pressurized cylinders or supply from cascade.
Priority valve on 3rd. filter bank output. (1800psi. set)
Pressure gauges on all 3 compressor stages to monitor cylinder output.
3/8 .049 tubing was used for control panel layout, providing solid interconnection between components to minimize the need to attach all the the components to the panel and "float" those difficult to attach on the tubing. With a little creative tubing bending, the number of connections were kept to a minimum. The panel is electrically grounded, since components, both electric and pneumatic were mounted to a sheet of 3/4" A/B plywood. Static ground to all P.V.C. piping.
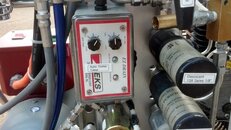
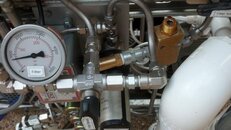
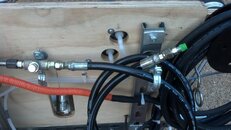
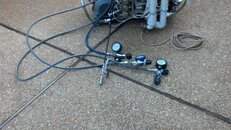
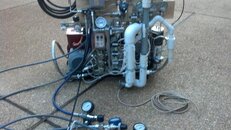
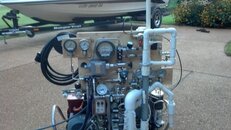
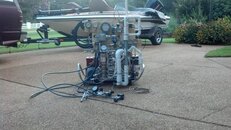
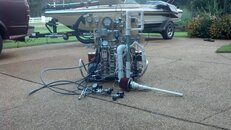
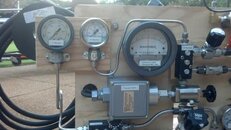
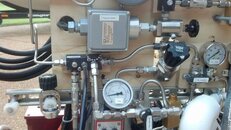
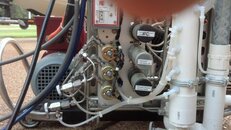
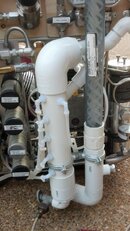
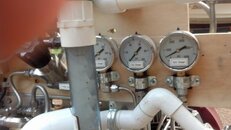
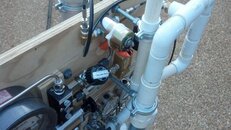
Last edited: